Structural health, usage and load monitoring
Expanding Aerospace and Defense solutions with Fiber Optic Sensing
The aerospace and defense sectors demand the highest levels of precision, reliability, and performance from every component and system. Traditional monitoring technologies often struggle to meet these stringent requirements, especially when dealing with advanced composite materials, dimensional limitations, extreme operating conditions, electromagnetic interference (EMI), and the need for lightweight structures.
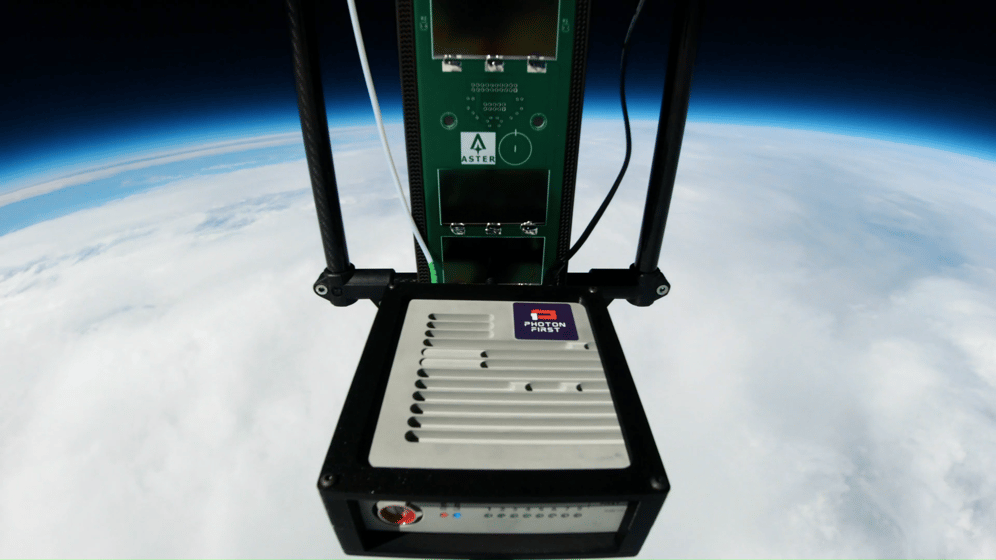
PhotonFirst addresses these challenges with cutting-edge Fiber Optic Sensing (FOS) solutions, providing a new dimension of insight into the structural health, usage, and loads of critical aerospace and defense assets. Our solutions are built upon Fiber Bragg Grating (FBG) technology, where optical fibers become the sensors themselves.
The optical fiber becomes the sensor with FBG-based technology
PhotonFirst's interrogators send light into an optical fiber containing FBG sensors. These sensors act like mirrors, reflecting specific wavelengths of light back to the interrogator. By analyzing the changes in the reflected light, precise measurements of parameters such as temperature, strain, pressure, and shape can be obtained. This process is enabled by photonics integrated chips (PICs), which are at the heart of PhotonFirst's innovative solutions.
Why Fiber Optic Sensing (FOS) works for Aerospace and Defense?
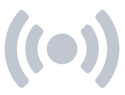
EMI-immune
Fiber based sensors are inherently immune to EMI (Electromagnetic Interference) and therefore enable for accurate data collection in the presence of strong electromagnetic fields.
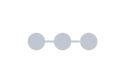
low footprint
Multiple sensing points on 1 fiber cable enable comprehensive light weight monitoring of critical components throughout the space crafts, airplanes, UAV's and USV's.
-1.png?width=97&height=95&name=Icons%20all%20(1)-1.png)
easier to install
Fiber based sensors are much smaller than conventional ones and demand for less cabling thanks to multiple sensing points on a single fiber cable.
.png?width=95&height=95&name=Accuracy%20%26%20reliability%20-%20PhotonFirst%20-%20Why%20(2).png)
High accuracy and reliability
Our sensors provide precise and reliable data even in the harsh environmental conditions encountered by aerospace and defence assets.

durability in harsh environment
Our sensors are designed to withstand the rigors of flights and various impacts, ensuring long-term performance and minimizing maintenance requirements.
Introducing the next generation Aerospace Interrogators - AGTR NEO & NG4
PhotonFirst is proud to introduce its latest advancement in Fiber Bragg Grating (FBG) interrogator technology, specifically designed to meet the rigorous demands of the aerospace and defense sectors. These new interrogators, the AGTR-NG4 and AGTR-NEO, represent a significant leap forward in precision, reliability, and adaptability for structural health monitoring and related applications.
Both the AGTR-NEO and AGTR-NG4 provide fast parallel sampling, high resolution sensing, integrated miniature single board computer for on-board data storage and processing. With their unique set of features, their reduced size, weight, and power specifications, both products provide an excellent FBG interrogator solution particularly suitable for harsh environments.
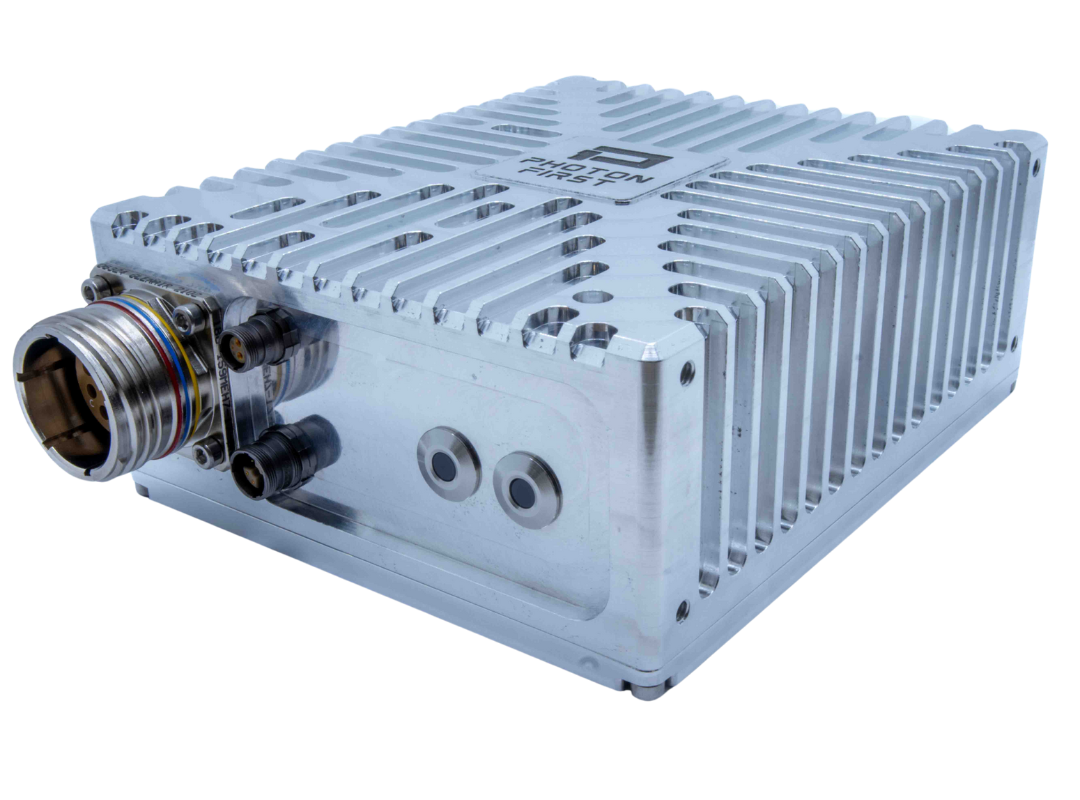
Key applications of FOS in aerospace and defense
PhotonFirst has a proven track record of applying FBG sensor technology across a wide range of aerospace and defense applications, with over 30 successful projects. These applications include:
Enhanced Structural Health Monitoring (SHM)
FOS is used to monitor the structural integrity of aircraft, spacecraft, UAV´s and defense platforms. This includes detecting damage and impact, measuring strain and stress, and monitoring wing deflection.
Payload Fairing monitoring
PhotonFirst's solutions are used to monitor the structural health of reusable payload fairings on space launchers, reducing inspection time and improving efficiency.
Rotor Blade monitoring
PhotonFirst has developed solutions for monitoring rotor blades in helicopters, such as the Apache. Our systems deliver critical data on blade structural health, airframe condition, and landing gear loads.
overheat detection
The small size of FBG sensors and multiplexing capability allow many of sensors to be integrated on a single fiber, enabling real-time thermal monitoring at multiple points — all with minimal cabling. This makes FBG-based systems ideal for harsh environments where precision and robustness are essential.
Landing gear load sensing
Fiber Optic Sensing technology can measure load and torque in aircraft landing gear, providing valuable data for reducing maintenance costs, improving fuel efficiency, and increasing safety.
Use cases
APACHE ROTOR BLADE MONITORING
Project objective
Implement Structural Health, Usage & Loads Monitoring System for the AH-64E Apache (SHULMS)
Solution
Construction of a customer specific interrogator (XGTR) with local data storage and integration of Fiber Optic Sensors in rotor blades.
Achievements
- Systems qualification against DO-160G
- Completed 18 months continuous flight monitoring
- Contactless Rotating Power and Data Transfer
- High speed data transfer (MIL-STD-1553)
- Follow up project: RNLAF Apache AH-64D FT and AH-64E demonstration
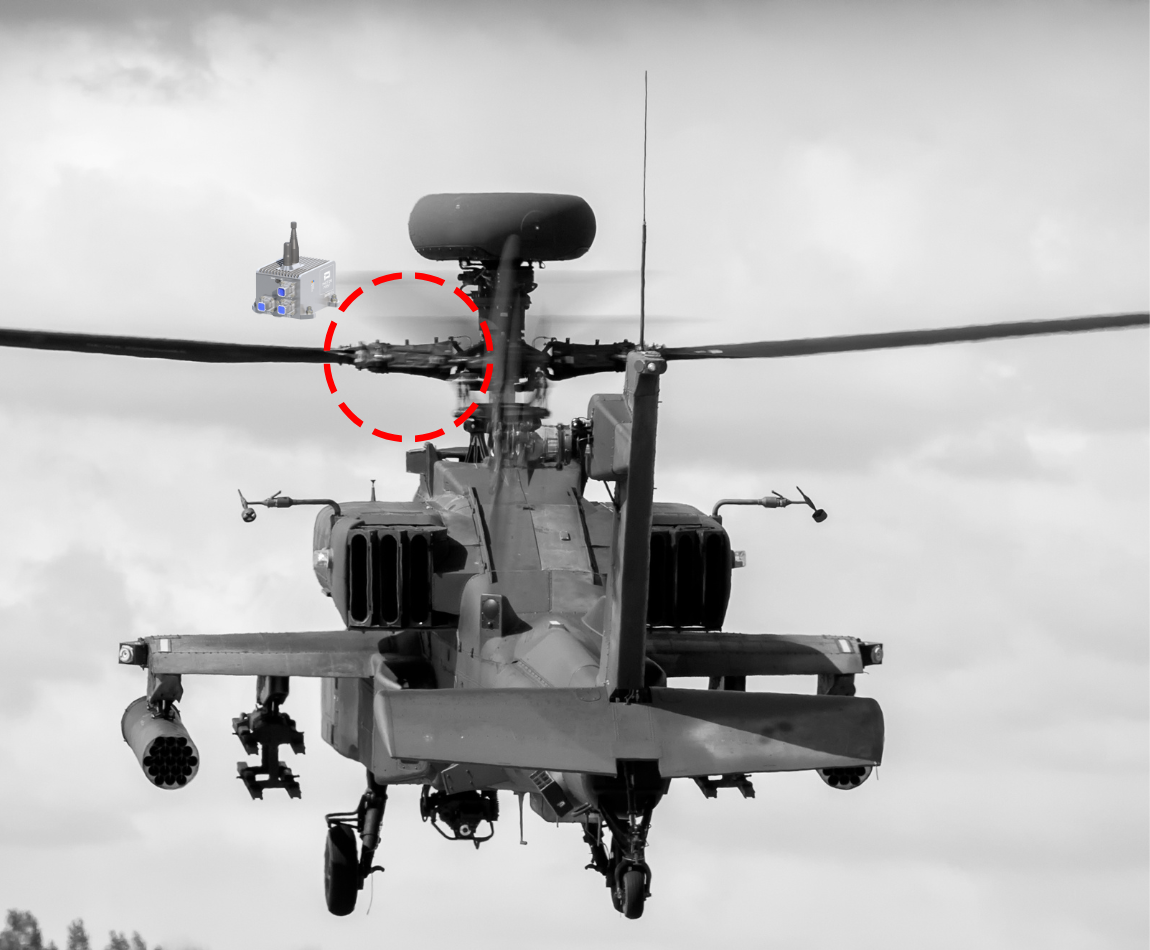
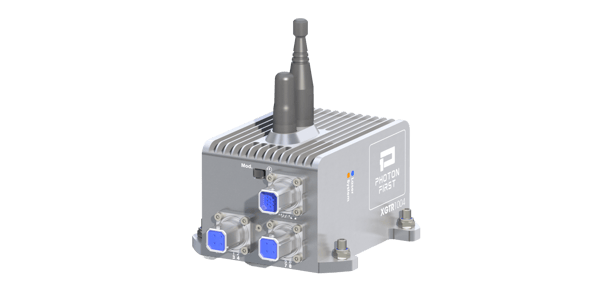
Project objective
- The Attila-project seeks to investigate and address the complexities of tiltrotor technology, particularly the aeroelastic phenomena that can affect their (forward) flight behavior.
- A key objective is to use advanced fiber optic sensor technology and contactless rotating power and data transfer techniques within this testbed.
Solution
PhotonFirst's FOS solutions are used to monitor structural health and loads within the tiltrotor testbed, offering advantages such as:
- Reduced the number of cables and components;
- Accurate and reliable data in harsh environments;
- Measuring strain, temperature, and shape.
Achievements
- Successful completion of dynamic characterization tests
- Wind tunnel testing of the testbed
- Ground vibration tests (GVT)
This demonstrates the successful application of advanced technologies, including fiber optic sensing, in a complex aerospace testing environment.
Project objective
- Test the satellite's resilience under near-space conditions
- Test the functionality of PhotonFirst's FBG sensor technology under near-space conditions
Solution
Installation of multiple sensors on 1 fiber cable and 1 interrogator measuring temperature, pressure and mechanical stress
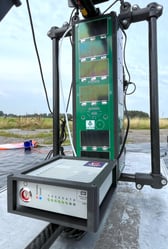
Achievements
The high-altitude balloon mission proved to be a great success. Icarus reached an impressive altitude of 34.8 kilometers before making a safe return, ‘only’ 250 kilometers from its lift-off area. More importantly, the mission effectively tested both the satellite's resilience and the functionality of PhotonFirst's FBG sensor technology under near-space conditions.
EUROPEAN AIRCRAFT RESEARCH PROJECTS
Advanced Landing Gear Sensing and Monitoring
The aviation industry needs an objective landing impact sensor. The EU-funded ALGeSMo project developed the world’s first such sensor, intended for commercial passenger aircraft. The sensor removes the subjectivity from landing assessments. If a landing was too hard, engineers will immediately know for certain.
Smart Intelligent Aircraft Structures
The project aimed to take Europe's aircraft industry to the next level by combining smart new design techniques to further cut development time and costs. Fiber optic sensors were integrated for Structural Health Monitoring of the fuselage.
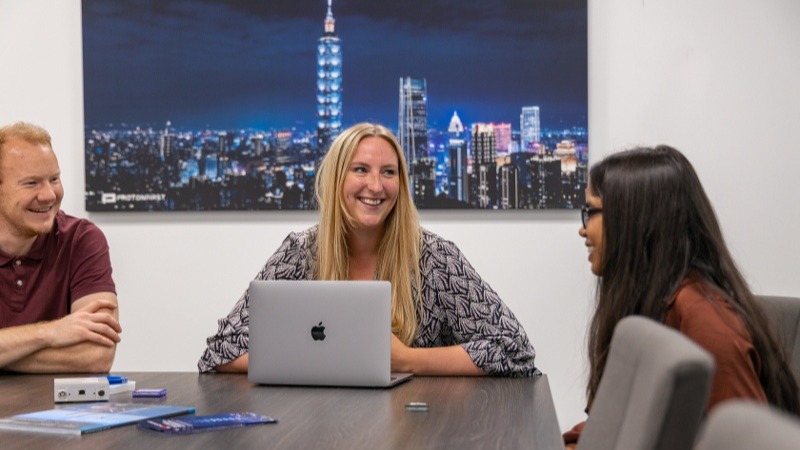