Structural load monitoring and performance optimization of Wind Turbines
Fiber Optic Sensing Solutions for the Wind Energy Sector
Wind energy plays a crucial role in the transition to a sustainable future. However, maximizing the efficiency, performance and lifespan of wind turbines requires advanced monitoring and diagnostic capabilities. PhotonFirst's fiber optic sensing solutions provide a significant advantage in this domain, offering unparalleled data accuracy and reliability for critical wind turbine applications.
With the integration of fiber optic sensing solutions in wind blades it is possible to maximize the return-on-investment of wind turbines, even for remote locations and at sea. In addition, (preventive) maintenance of wind turbines can be planned well ahead, reducing operations costs.
Why Fiber Optic Sensing (FOS) in Wind Turbines?
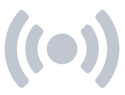
EMI-immune
Fiber based sensors are immune to EMI (Electromagnetic Interference) and therefore enable for accurate data collection in the presence of strong electromagnetic fields
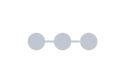
low footprint
Multiple sensing points on 1 fiber cable enable comprehensive monitoring of critical components throughout the turbine, including the wings, gearbox, generator and the tower itself.
-1.png?width=97&height=95&name=Icons%20all%20(1)-1.png)
easier to install
Fiber bases sensors are much smaller than conventional ones and demand for less cabling thanks to multiple sensing points on a single fiber cable.
.png?width=95&height=95&name=Accuracy%20%26%20reliability%20-%20PhotonFirst%20-%20Why%20(2).png)
High accuracy and reliability
Our sensors provide precise and reliable data even in the harsh environmental conditions encountered by wind turbines.

durability in harsh environment
Our sensors are designed to withstand the rigors of wind turbine operation, ensuring long-term performance and minimizing maintenance requirements.
Key applications of FOS in Wind Turbines
Enhanced Structural Health Monitoring
Blade Monitoring: Fiber optic sensors can be embedded within wind turbine blades to monitor strain, vibration, and temperature. This enables early detection of fatigue, cracks, and other structural issues, allowing for proactive maintenance and extending the lifespan of blades.
Tower Monitoring: Sensors can be integrated into the tower structure to monitor strain and vibration, providing valuable insights into potential structural weaknesses and ensuring the safety and stability of the turbine.
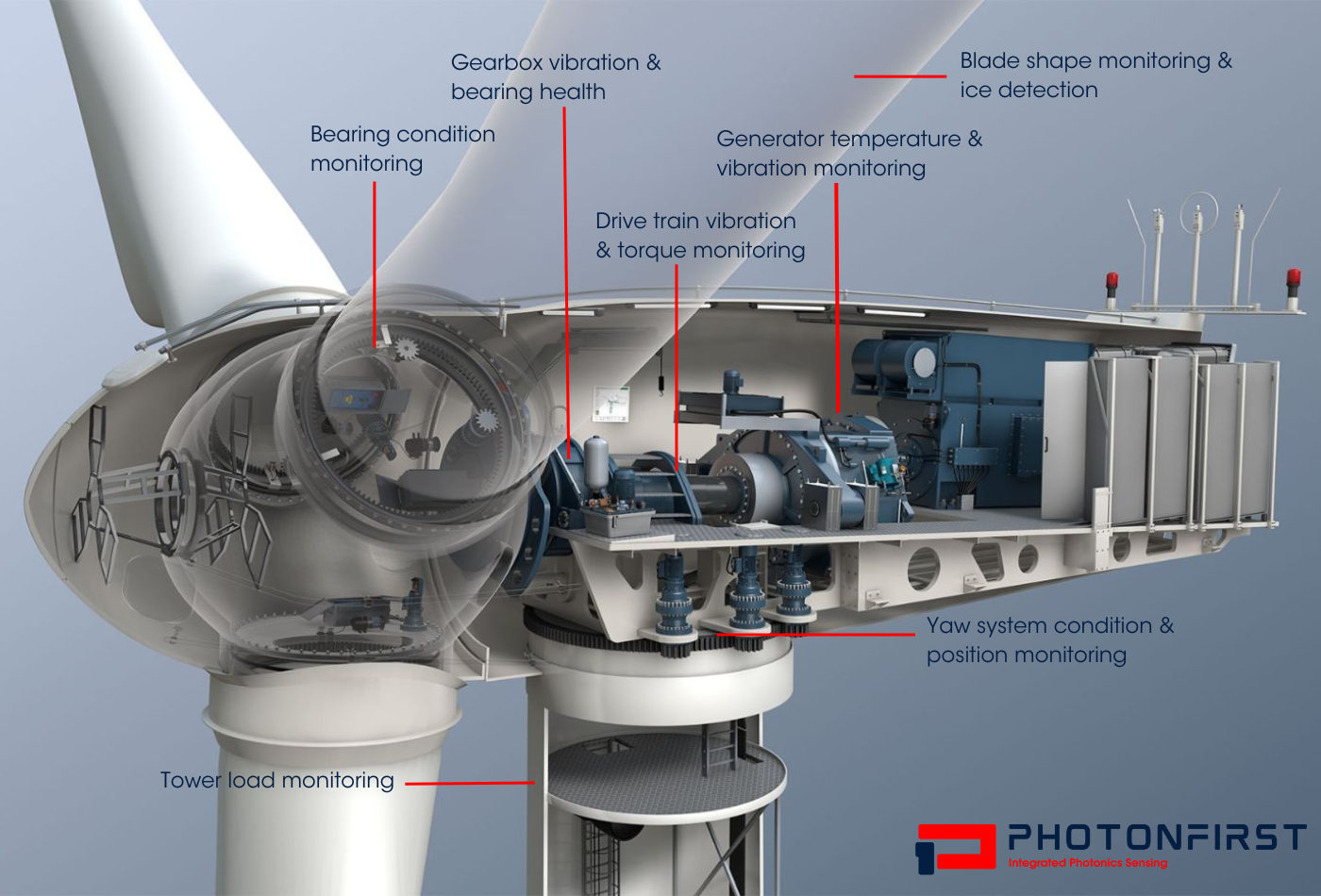
Improved Operational Efficiency
Gearbox Monitoring: Fiber optic sensors can monitor vibrations and temperature within the gearbox, enabling early detection of anomalies that could lead to costly failures
Generator Monitoring: Real-time monitoring of temperature and vibration within the generator can help optimize performance and prevent overheating
Enhanced Safety
Ice Detection: Fiber optic sensors can be used to detect the formation of ice on blades, allowing for timely de-icing procedures and preventing damage to the turbine.
Fire Detection: Fiber optic sensors can be integrated into fire detection systems, providing early warnings and enabling rapid response to emergencies.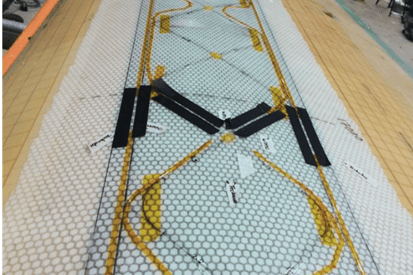
blog - HOW INTEGRATED PHOTONICS SENSING CAN HELP WIND TURBINE OPERATORS IMPROVE RETURN ON INVESTMENT
Competition among wind farmers to make winning bids in tenders for new generation contracts while maintaining a healthy return on investment is spurring innovation in operating technology. Turbine operators are learning that advanced photonic sensing can provide more detailed, real-time wind turbine monitoring data, informing them about the behavior and performance of key components such as blades, towers, gearboxes and cabling.
Use cases
Project objective
Improving fibre composite blade design for Tidal Turbine OEM by monitoring blade behaviour during operation.
Solution
Fibers can be integrated into the blades without affecting structural integrity and ‘aquadynamics’ of the blades
Achievements
- Full fiber optic sensing system delivery, containing 2 X 48 FBGs installation and testing
- Communication via optical rotary joint. Or integrated interrogator
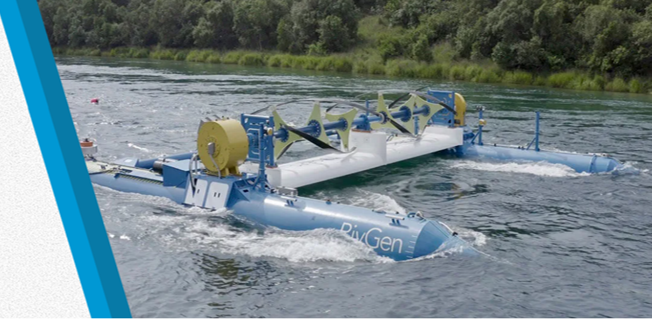
Source: ORPC